As a kind of typical solid lubricant materials, copper–graphite (Cu/Gr) composite is environmental friendly and has a variety of applications in engineering. Therefore, the investigation on its tribological properties and application in sliding bearings, electrical brushes, and other components which serve under sliding and oil-free lubricated conditions is of great significance.
Researchers of the R&D Center of Lubricating and Protecting Materials of the Lanzhou Institute of Chemical Physics (LICP), CAS, have carried out a series of studies on the tribological properties of Cu/Gr composite, namely effect of surface texture on transfer layer formation and tribological behavior of Cu/Gr composite and effect of sliding speed on surface modification and tribological behavior of Cu/Gr composite.
Metal matrix composites (MMC) containing graphite particulates usually have reduced friction under dry sliding, which is closely dependent on the formation of continuous transfer layer on the sliding surface of counterpart. The transfer process, understandably, may be affected by the actual variance of texture on counterpart surface. Thus the transfer behavior of Cu/Gr composite onto steel discs with different textures was investigated, where the evolution of the transfer layers on the counterparts with different textures under both low and high loads was highlighted. It was found that the textures had different ratcheting effects on the contact surface of Cu/Gr composite, which led to diverse extent of extruded surface layer and size of extruded sliver. Moreover, fractured sliver acted as the precursor of the transfer layer and played a key role in determining the continuity of the transfer layer, which in turn led to different friction and wear behavior of the composite sliding against steel counterparts with different textures.
As for the effect of sliding speed on friction and wear performance of Cu/Gr composite, the results show that: 1. the friction coefficient and wear rate of Cu/Gr composites are largely dependent on sliding speed. When the speed exceeds the critical value (0.5 m/s in the present observation), a transition of the friction and wear regime occurs; 2. the formation of a lubricant layer on the contact surface is regarded as an important characteristic for the good tribological performance of Cu/Gr composites. Due to a large strain gradient in subsurface deformation zone, the graphite-rich lubricant layer can easily form on the sliding surface when the speed is lower than the critical value. At speeds exceeding the critical value, however, formation of the lubricant layer is difficult due to the delamination wear by the high strain rate; 3. the wear mechanism is found to be mild wear caused by ratchetting at speeds less than the critical value and severe wear induced by delamination at speeds exceedingthe critical value.
The work has received support from the National Natural Science Foundation of China. The findings have been published in Wear (Wear 270 (2011) 218–229 ) and Tribol Lett (Tribol Lett (2011) 41:363–370)。
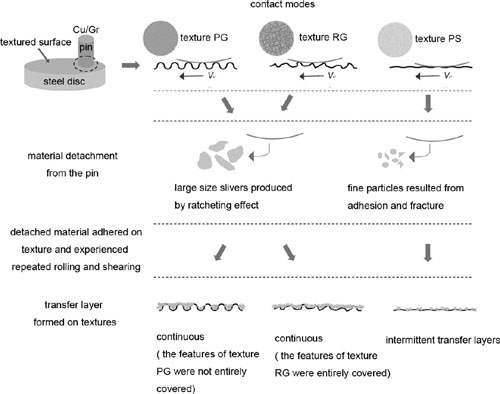
A schematic process of transfer layer formation (Image by LU Jinjun et al.)
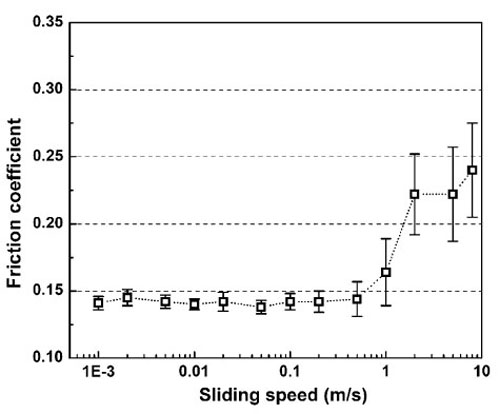
Average friction coefficient at different sliding speeds (Image by LU Jinjun et al.)
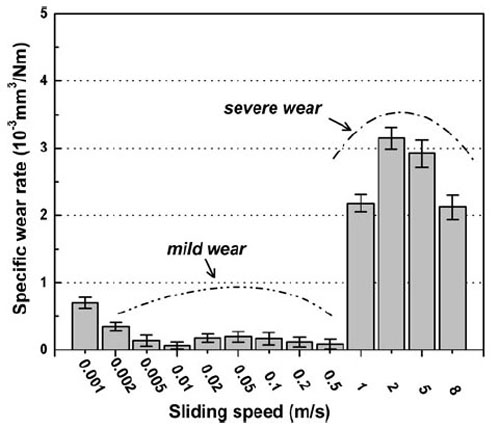
Variation in the wear rate of Cu–Gr with speed (Image by LU Jinjun et al.)
WearPaper
Tribol LettPaper
Prof. LU Jinjun's homepage