Ceramic lubricating materials are low in thickness, thermally stable and have ideal structure. They can improve the anti-erosion, anti-frication, high-temperature resistant and anti-oxidative properties of lubricating materials. However, the application of ceramic materials in high temperature lubrication has been limited due to their brittleness and poor mechanical property resulted from tribological design. Therefore, to overcome the conflict between their mechanical and tribological properties and improve their tribological property while maintain ideal structure has become a problem to be urgently solved.
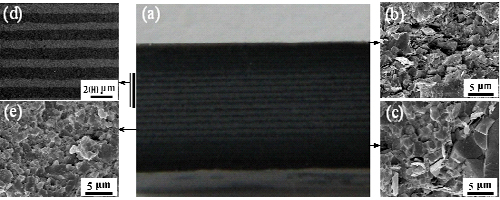 |
Microstructure of the material (Image by HU Litian at al.) | The researchers at R&D Center of Lubricating and Protecting Materials, Lanzhou Institute of Chemical Physics (LICP) of the Chinese Academy of Sciences (CAS), have developed a new design method to achieve the integration of structure and lubricating function in ceramic.Complying with the design principle of bionic and graded composites, they have prepared Al2O3/Al2O3–ZrO2(3Y)/SL composites with laminated-gradient structure and studied their mechanical and tribological properties The results show that this newly-developed ceramic composite achieves satisfactory strength and tribology properties compared with the traditional ceramic self-lubricated composites. The bending strength, which was five times higher than that of traditional Al2O3 self-lubricated composites, reached the same level as the properties of general monolithic Al2O3 ceramics. In the temperature range of 25–800℃, the friction coefficient of Al2O3/Al2O3–ZrO2(3Y)/SL composite was less than 0.54, which was about half of that of monolithic Al2O3 ceramics. These excellent tribological and mechanical properties indicate that the composite material can have numerous hightechnology applications as a structural material. The work has received support from the National Program on Key Basic Research Project of China (973 Program), National Natural Science Foundation of China (NSFC) and West Light Foundation of the Chinese Academy of Sciences. The findings have been published in COMPOSITES PART B-ENGINEERING (2013,47:145) and MATERIALS & DESIGN(2013, 49: 421). |