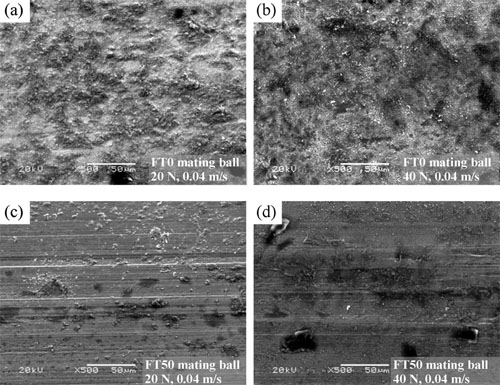
SEM images showing the morphologies of the worn surfaces of AISI 52100 steel ball mating with the FT0 and FT50 at applied loads of 20N and 40N with a sliding speed of 0.04 m/s after sliding for 20 min
Researchers at the R&D Center of Lubricating and Protecting Materials of the Lanzhou Institute of Chemical Physics (LICP) have studied the effect of TiC contents on dry-sliding tribological properties of the Fe–28Al–5Cr intermetallic composites and to delineate the wear mechanisms.
They first produced the Fe–28Al–5Cr and its composites containing 15, 25, 35, 50 wt.% TiC, by hot-pressing process and investigated their tribological performance against an AISI 52100 steel ball in ambient environment at varying applied load and sliding speed.
It is found that 1) the wear rates of the materials decrease with increasing TiC content at identical sliding parameter, demonstrating that the addition of hard TiC improves significantly the dry-sliding wear resistance of Fe–28Al–5Cr in ambient environment, which is attributed to the higher hardness of the composites and supporting role of hard TiC phase. It is worth noting that the wear rate of the FT50 is 4–30 times lower than that of the FT0. Wear rates of all the materials increase with increasing applied load, while is irrespective of sliding speed. Wear rates of all the materials are in the magnitude of 10−4–10−3mm3m−1. Friction coefficients of all materials are in the range of 0.46–0.60 and are independent of the TiC content and applied load, but increase with increasing sliding speed. The dominant wear mechanism of the Fe–28Al–5Cr and 15% composite is flaking-off, but those of the 25–50% composites are flaking-off and plowing.
Fe3Al alloy have been considered the material for a series of anti-wear applications to replace conventional wear resistance cobalt-based alloys and iron-based alloys containing chromium and manganese. There is much work dedicated to Fe3Al alloy. However, to the authors’ knowledge, there are few studies reported on the tribological properties on Fe3Al–TiC composites.
The work ahs received support from the National Natural Science Foundation of China and the National Program on Key Basic Research Project of China (973 Program) and the Innovation Group Foundation from NSFC.
The findings have been published in Wear (Wear 271 (2011) 881– 888).
WearPaper