Due to its high melting point, high thermal conductivity, low density, and excellent oxidation resistance, NiAl intermetallic compound is regarded as potential high temperature structural material having promising application in gas turbine engine rotor blades and stator vanes. However, its application as an engineering material is limited by poor ductility at room temperature and low strength at elevated temperature.
Researchers at R&D Center of Lubricating and Protecting Materials, Lanzhou Institute of Chemical Physics (LICP), Chinese Academy of Sciences (CAS), have synthesized Nickel aluminide (NiAl) intermetallic compound coatings by laser cladding and investigated the effects of laser cladding parameters on the phase composition, microstructure and wear resistance of the resulting NiAl coatings.
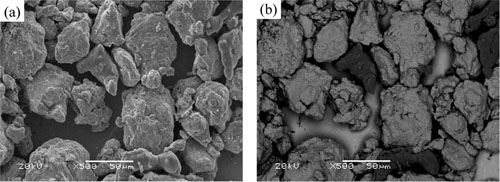 |
Morphologies of the mixed powders of Ni and Al: (a) bright-field SEM micrograph; and (b) backscattered SEM micrograph. |
It has been found that laser power density had a crucial influence on the microstructure and friction and wear behavior of NiAl coatings. Namely, the NiAl coatings synthesized under a lower power density have more dense and fine microstructure, and lower friction coefficient and wear rate. Besides, the friction and wear behavior of the laser cladding NiAl coatings is highly dependent on applied normal load and sliding speed; and the resulting coatings sliding against Si3N4 in a ball-on-disc contact mode is more suitable for tribological application at a moderate normal load of 3–7 N and sliding speed of 0.16–0.21 m/s.
The work has received support from the National Natural Science Foundation of China (NSFC), Innovative Group Fund from NSFC and National Program on Key Basic Research Project of China (973 Program). The findings have been published in Wear(Wear274– 275 (2012) 298– 305).