High-temperature solid lubricants have shown much potential for applications to sliding parts in a large number of industrial applications, such as those encountered in the tooling, materials-forming, auto-motive, and nuclear power industries. However, at about 500℃, conventional solid lubricants, such as graphite and molybdenum disulfide are oxidized in air and lose their lubricating effects. It is essential to search for efficient solid lubricants that can serve at even higher temperature.
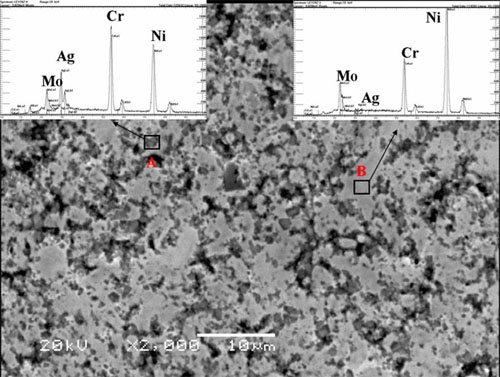 |
SEM micrographs and EDS results of the NC20AM Ni-based composite |
Researchers at State Key Laboratory of Solid Lubrication, Lanzhou Institute of Chemical Physics (LICP), Chinese Academy of Sciences (CAS), have fabricated the Ni-based self-lubricating composites with addition of 10 and 20 wt% Ag2MoO4 by powder metallurgy technique, and investigated the effect of Ag2MoO4 on tribological properties from room temperature to 700℃.
The results show that the Ag2MoO4 decomposed into Ag and Mo during the high-temperature fabrication process. The friction coefficient and wear rate of the composites decrease with the increasing of temperature and Ag2MoO4 contents and the composites with addition of 20 wt% Ag2MoO4 exhibits the lowest friction coefficient (0.26) and wear rate (1.02 ⅹ10-5 mm3 N-1 m-1) at 700 ℃. The composition of the tribo-layers on the worn surfaces of the composites is varied at different temperatures. It is proposed that the improving of tribological properties of the composites at high temperatures are attributed to the synergistic lubricating effect of silver molybdate (reproduced in the rubbing process at high temperatures) and Fe oxide (transfer from disk material to the pin) formed on the worn surface.
The work has received support from the National Natural Science Foundation of China . The findings have been published in Tribol Lett(Tribol Lett(2012) 47:21–30).